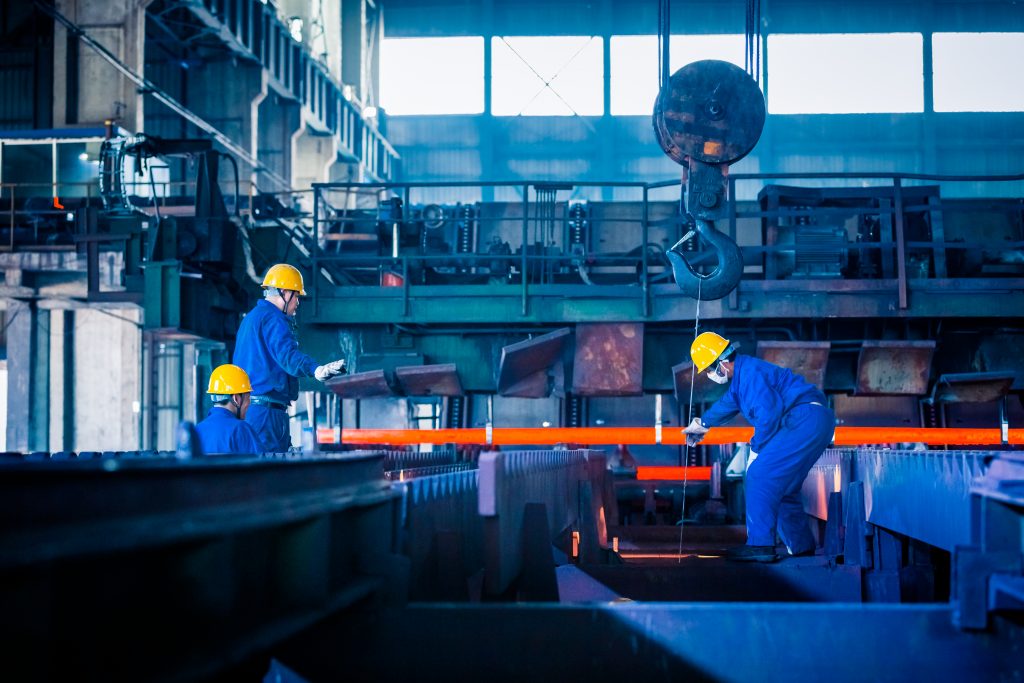
Total Quality Management has its roots in industrial engineering disciplines. The concept originated when Walter Shewhart developed the statistical process control and applied it to product quality control. It was adopted and further developed in Japan in 1940s when Edward Deming and Joseph Juran visited the country and applied the method to increase the quality of products while also involving everyone in the organization. Shown below is Deming’s idea of TQM: The successes of TQM in various sectors are well documented. In recent years, TQM has been attracting attention among public sector organizations as citizens become more demanding of governments to do more with less. In Japan, for example, the government has adopted the PDCA (plan, do, check, action) cycle and it has since become part of the policy formulation process. TQM is a holistic management approach to long-term success through customer satisfaction. The focus is on improving the quality of outputs, either goods or services, through continual improvement of internal processes. Apart from implementing new methods and software solutions, TQM also requires a change in culture. However, many organizations are unable to start this transformation unless they are faced with a disaster or are forced by their customers. There are five basic principles of TQM.
- Quality oriented – The mission and vision of the organization must be balanced with its own needs and of the citizens. The leadership must have a political will to establish policies that are supportive of TQM.
- Customer focused– One of the goals of TQM is to ensure that you meet and exceed customer’s satisfaction. In defining its processes and functions, the organization must always consider its customers’ point of view.
- Total employment involvement – Top management support is imperative and is pivotal in the implementation of TQM. In addition, the role of the employees in TQM is very different from the traditional view. TQM employees are empowered to make decisions, and their suggestions and contributions are highly valued by the management.
- Continuous process improvement – TQM revolves around the philosophy of never ending improvement. Since the customers’ expectations are always changing, there is a need to always improve results in all aspects of work, to harness the capabilities of the employees, and to enhance processes and technology.
- Performance measures – An organization should manage its TQM initiatives based on facts and not on gut feelings. There must be an established baseline to assess the results from improvement.
In implementing TQM in the public sector, factors such as political environment, financial limitations, and old paradigms must be addressed first. The focus should not be on short term but on long term goals with cohesive vision of systemic change. Most importantly, the success of TQM hinges on the improvement of the whole organization and not just the performance on selected components.