Some of the most common problems at a workplace are inconsistent cleanliness and orderliness, difficulty in retrieving files, inadequate space, and improper storage of files and things. 5S is a systematized approach that helps address these problems. It also helps in achieving greater organization, standardization and efficiency, all while reducing costs and boosting productivity. In 1972, Henry Ford used the CANDO programme (Cleaning up, Arranging, Neatness, Discipline, and Ongoing improvement) and this technique was later popularized in Japan as 5S methodology by Hiroyuki Hirano.
What is 5S? 5S stands for five phases each named after a different Japanese term beginning with the letter “Sâ€: seiri, seiton, seiso, seiketsu, and shitsuke.
- Seiri (Sort) – In this step, you sort items that are necessary and unnecessary. Items that do not belong in the working area must be disposed properly. In addition, items that are not needed or may be needed in the future must be red-tagged and placed in a holding area.
- Seiton (Systematize) – Here you organize necessary items for easy and fast retrieval
Some seiton practices include:
- Following the first-in-first-out method for storing item;
- Assigning each item a dedicated location;
- Systematic labelling of all items and their locations;
- Making items visible to reduce searching time; use color-coding;
- Arranging items so they can be reached or handled easily;
- Separating special tools/devices from common ones
- Placing frequently used tools/devices near the user
- Fixing unstable article for safety; and,
- Keeping space for safety equipment and evacuation passages clear.
- Seiso (Sweep) – Seiso is thoroughly cleaning the work area, including tools, machines and other equipment. Doing seiso ensures that everything is in good condition and is ready to be used when needed.
- Seiketsu (Sanitize/standardize) – Seiketsu involves maintaining a high standard of housekeeping and workplace organization at all times. You keep each area consistent with one another and ensure that conditions do not deteriorate to their former state.
- Shitsuke (Self-discipline) – This entails doing things spontaneously without being told or ordered and training people to follow good housekeeping rules. Instilling discipline is critical to avoid backsliding.
Some shitsuke practices involves:
- Greeting people with a smile;
- Being a good listener;
- Demonstrating team spirit;
- Being professional in your conduct and dealings with others;
- Putting things back in their proper place after use;
- Being punctual;
- Always keeping your workplace clean and tidy;
- Following safety rules strictly;
- Wearing clean uniform/office attire and shoes; and,
- Observing proper office decorum.
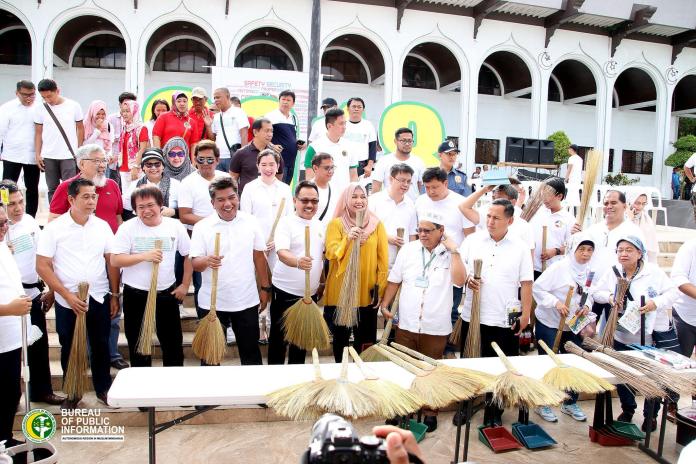
Digital 5s. Implementing 5s is not limited to physical space. Electronic storage areas such as servers and hard disks should also be organized to ensure that everyone can easily access the files that they need. To do a digital 5s, a filing policy must be created to know which documents must be kept for what period of time. Every employee will go through all his/her electronic files to determine which ones can be deleted and which ones can be kept. Next step is to give each file/folder a logical place. There must also be a standardized way of naming the documents. Cleaning of servers and hard disks must be done on a regular basis. It is equally important to make sure that everyone sticks with the system. Apart from these, always keep the office’s electronic storage space user-friendly and easy to navigate.
Benefits of 5S methodology. Among the main benefits of implementing 5S are:
- Work stations become cleaner, safer, well-organized and more pleasant;
- Floor space utilization is improved;
- Workflow becomes smoother and more systematic;;
- Time for searching tools, materials and document is minimized;
- Machine breakdowns are reduced since clean and well-maintained equipment breaks down less frequently. It also becomes easier to diagnose and repair before breakdowns occur, therefore extending equipment life;
- Errors are minimized;
- Consumables and material wastage are minimized;
- Morale and satisfaction of employees improves; and,
- Productivity improves simultaneously with the quality of products and services.