Purpose: Waste Reduction, Streamlining, Continuous Improvement
About the Tool
The Visual Factory concept comes from early Lean Manufacturing practices of the Toyota Production System (TPS). Toyota utilized visual signals to streamline operations, focusing on waste reduction and enhancing workflow. While they weren’t the only Lean practitioners to employ visual tools, they have been (and continue to be) the most notable and influential figures in Lean Manufacturing over the past century. Toyota took basic visual tools to a higher level by not only clarifying their purpose but also outlining when and how to use them for optimal impact.
The phrase “visual factory techniques” refers to a concept in lean manufacturing that relies on visual information present throughout a workplace. It utilizes a variety of communication tools to share information precisely when and where it is needed. By using visual controls, it becomes possible to convey messages without the need for verbal communication and to disseminate information seamlessly. These visual tools are also beneficial for enhancing productivity, as employees access the information they require exactly at the right moment and location.
Application in the Public Sector
Even though the manufacturing sector is where the Visual Factory principles originated, they have recently been successfully adapted within the public sector to improve service delivery and operational transparency. For example, government offices implemented visual management boards for tracking the status of public service requests, with both employees and citizens being able to follow the progress in real-time. In the case of hospitals, visual cues are employed to manage patient flow, hygiene protocols, and equipment availability for improved patient care and safety. These applications highlight the versatility of visual management to foster efficiency and accountability within public service.
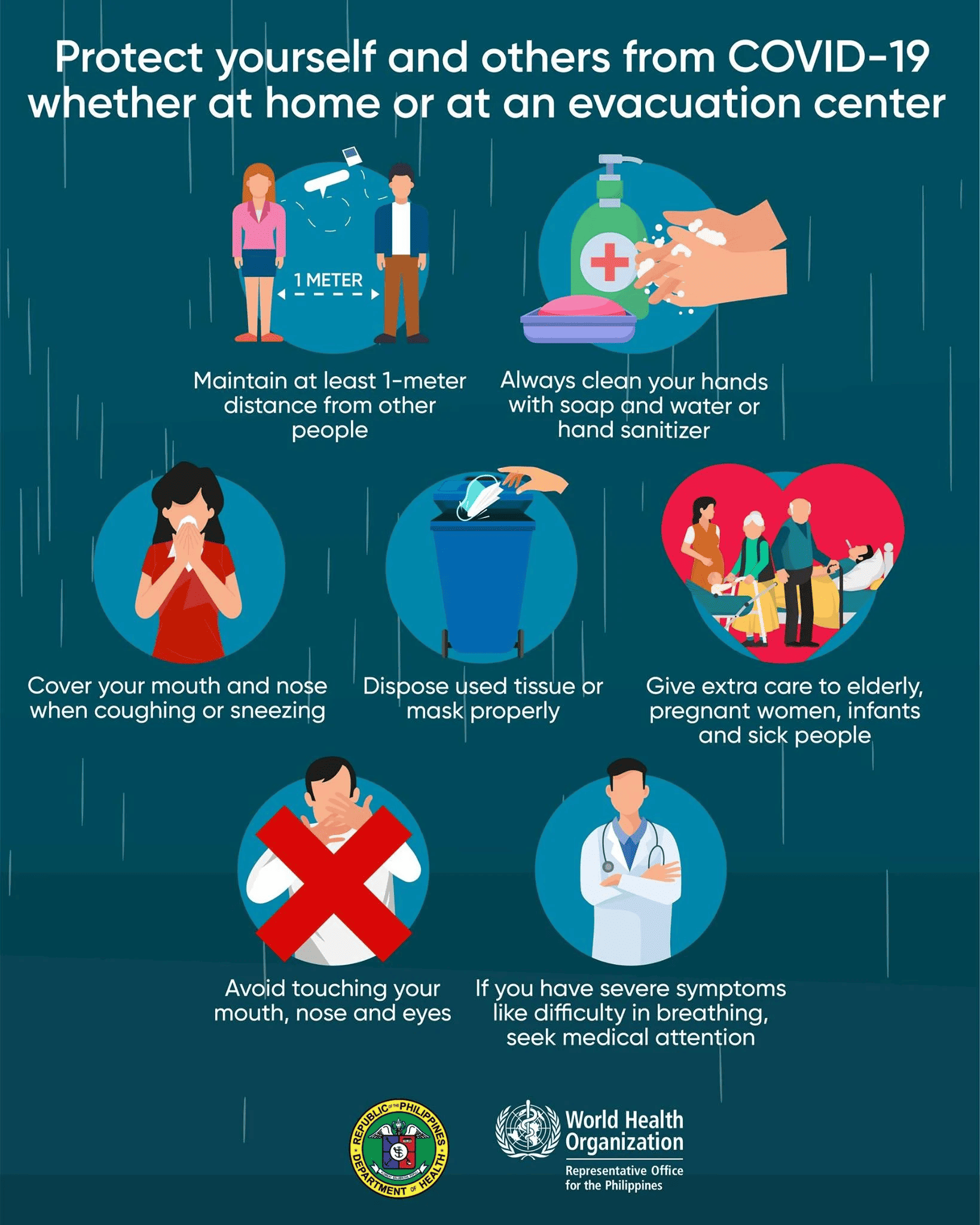
Sample DOH Visual Guide regarding COVID Protocols
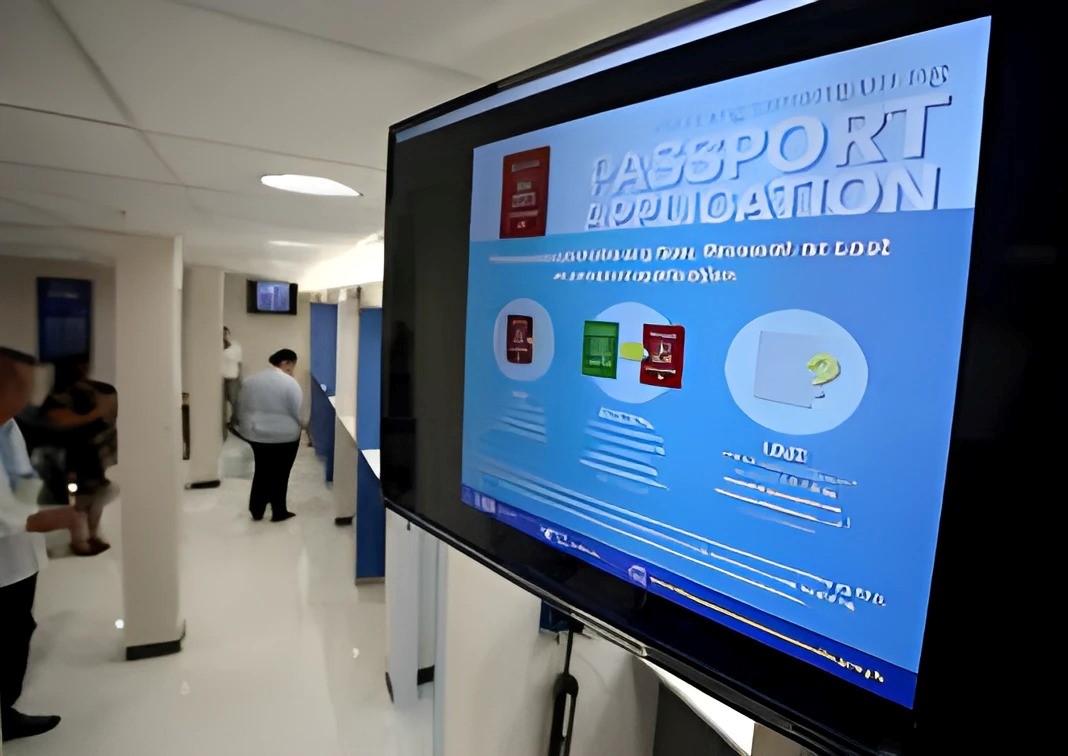
Sample DFA office using Visual Instructions in Passport Application
Key Benefits
- Enhanced Communication: Visual aids cut over language barriers and simplify the representation of complex information, thus guaranteeing that all employees across the board have a clear understanding of processes and expectations.
- Increased Efficiency. Visual management mitigates downtime by providing instant access to essential information while expediting decision-making.
- Improved Safety. Safety protocols and danger signs are detected easily, thereby preventing accidents at the workplace, as well as ensuring compliance with safety regulations.
- Employee Engagement. Resourcefulness remains key in order to think beyond the traditional ways of doing things.
- Transparency and Accountability. Having publicly available performance metrics and project statuses shows transparency where progress can be known, and responsibilities are transparent.
How to Use the Tool
Here are some of the fundamental steps in implementing Visual Factory:
- Identify Areas and Needs. Start with an assessment of areas that would benefit in your operations from visual management. Identify those processes where missing information or miscommunication happens more often than not.
- Standardize Visual Tools. Create a unified set of visual aids such as signs, labels, color codes, etc., that comply with your organization’s standards, and which are easily interpreted by all the employees.
- Integrate Visuals into Workspaces. Visual tools should be installed strategically in the workplace so that they will be visible and accessible for this purpose-the process flowchart placed at the workstation, floor markings to define work areas, and digital dashboards to view real-time performance metrics.
- Educate and Train Employees. Conduct training sessions with employees for better understanding of the visual management system as well as to know the significance and interpretation of each visual element.
- Continuous Improvement. This entails constant review and modification of visual tools in line with feedback and constantly evolving operational requirements for the continued effectiveness of such tools
References:
- Latest Quality. (2018, March 29). Visual factory techniques and how to implement them. Latest Quality. https://www.latestquality.com/visual-factory-techniques/
- Greatbanks, R., & Manville, G. (2015). Visual performance management: Does it work in public service organisations? UEA Digital Repository. https://ueaeprints.uea.ac.uk/id/eprint/74858/1/Accepted_Manuscript.pdf
- Kyzentree. (2021, January 29). Visual factory benefits. Kyzentree. https://www.kyzentree.com/visual-factory-benefits/
- Hessing, T. (n.d.). Visual factory. Six Sigma Study Guide. https://sixsigmastudyguide.com/visual-factory/
- Fogwing. (2025, February 1). Understanding visual factory: A comprehensive introduction. Fogwing.io. https://www.fogwing.io/blog/industrial/what-is-visual-factory/