Purpose: Risk Management
Target Participants or Users: Project Managers, Auditors, Safety Officers, Planning and Control Officers, Procurement Officers, Risk Management Officers
About the Tool:
Failure Modes and Effects Analysis (FMEA) is a reliability tool originally developed for manufacturing to identify and minimize potential failures before they occur. It is a structured method that pinpoints potential failure modes, their causes and consequences, and guiding actions to either prevent or correct them. Its use has now expanded into the service sector. Previous research, however, has been mainly conceptual, lacking practical guidelines tailored specifically for services.
When applied to government services, FMEA can significantly improve efficiency, reliability, and citizen satisfaction by proactively addressing risks and vulnerabilities. FMEA can also help identify and address failures in government services like public healthcare, tax administration, emergency response, and licensing and permits by automating processes, analyzing potential failures, and creating contingency plans to improve citizen satisfaction.
How to Use the Tool:
Steps
1. Select a service process to analyze and understand all components and their functions. Choose a process that is known to be problematic in your facility or one that is known to be problematic in many facilities.
2. Select a cross-functional team from the affected work groups that can help complete the FMEA.
3. Outline the process. Clearly specify the steps involved so that every team member understands what is being analyzed
4. Gain consensus on the ranking criteria for severity, occurrence and detection. The table below shows the commonly used rating guidelines.
Severity | Severity Ranking | Probability of Failure | Ranking | Detection | Detection Ranking |
Hazardous without warning | 10 | Very high; Failure is almost inevitable (>1 in 2) | 10 | Absolute uncertainty | 10 |
Hazardous with warning | 9 | 1 in 3 | 9 | Very remote | 9 |
Very high | 8 | High; Repeated failures (1 in 8) | 8 | Remote | 8 |
High | 7 | 1 in 20 | 7 | Very low | 7 |
Moderate | 6 | Moderate: Occasional failures (1 in 80) | 6 | Low | 6 |
Low | 5 | 1 in 400 | 5 | Moderate | 5 |
Very low | 4 | 1 in 2,000 | 4 | Moderately high | 4 |
Minor | 3 | Low; relatively few failures (1 in 15,000) | 3 | High | 3 |
Very minor | 2 | 1 in 150,000 | 2 | Very high | 2 |
None | 1 | Remote: Failure is unlikely (<1 in 1.5 million) | 1 | Almost certain | 1 |
Figure 1. FMEA: Ranking of Potential Failures.
5. Draw the process flowcharts and describe the functions of each component.
6. Identify necessary inputs to the process, such as materials, method, technology, and people actions. Anticipate and list all potential failure modes for each input at various steps in the process. You can identify the root causes of each failure mode using a cause-and-effect diagram.
Occurrence (1–10): On a scale of 1-10, with 10 being the most likely, what is the likelihood the failure mode will occur?
7. Evaluate the severity of the effect of the potential failure mode.
Severity (1-10): On a scale of 1-10, with 10 being the most likely, what is the likelihood that the failure mode, if it does occur, will cause severe harm?
8. Identify the current controls and rate the detection. List the current controls in place to mitigate or prevent failure (e.g. Training programs, Visual inspection).
Detection (1-10): On a scale of 1-10, with 10 being the most likely NOT to be detected, what is the likelihood the failure will NOT be detected if it does occur?
9. Calculate the Risk Priority Number (RPN) to prioritize which failures require immediate attention. RPN is calculated by multiplying the Severity, Occurrence and Detection rankings for each potential failure / effect, cause and control combination. The lowest possible score will be 1 and the highest 1,000. To calculate the RPN for the entire process, simply add up all of the individual RPNs for each failure mode.
RPN = Severity x Occurrence x Detection
10. Identify the failure modes with the top 10 highest RPNs. Failure modes with high RPNs should be prioritized for attention, as they are likely to have the most significant impact on the process. On the other hand, failure modes with low RPNs are unlikely to substantially affect the process, even if eliminated, so they should be given lower priority.
11. Plan actions that mitigate the risks associated with failure modes:
a) If a failure mode is likely to occur:
- Analyze the causes and determine if any or all of them can be eliminated.
- Consider implementing a forcing function, such as a physical constraint that prevents errors.
- Introduce verification steps, like independent double-checks, bar coding on medications, or alert screens.
- Modify related processes that contribute to the causes.
b) If the failure is unlikely to be detected:
- Identify prior events that could serve as “flags” indicating the potential for the failure mode.
- Add a step to the process that intervenes at the earlier event to prevent the failure mode.
- Implement technological alerts, such as devices with alarms that notify users when values are approaching unsafe limits.
c) If the failure is likely to cause severe harm:
- Identify early warning signs that a failure mode has occurred and train staff to recognize them for early intervention. For example, conduct drills to simulate events that could lead to failure, helping staff improve their ability to spot early warning signs.
- Provide relevant information and resources.
12. Designate a responsible person to implement the recommended actions.
13. Document the actions completed and reassess the RPN. Measure the success of process changes. Like all improvement projects, the success of improvement actions is evaluated.
Sample Failure Mode and Effect Analysis (FMEA) Template and Actual FMEA
Sample Failure Mode and Effect Analysis (FMEA) Template
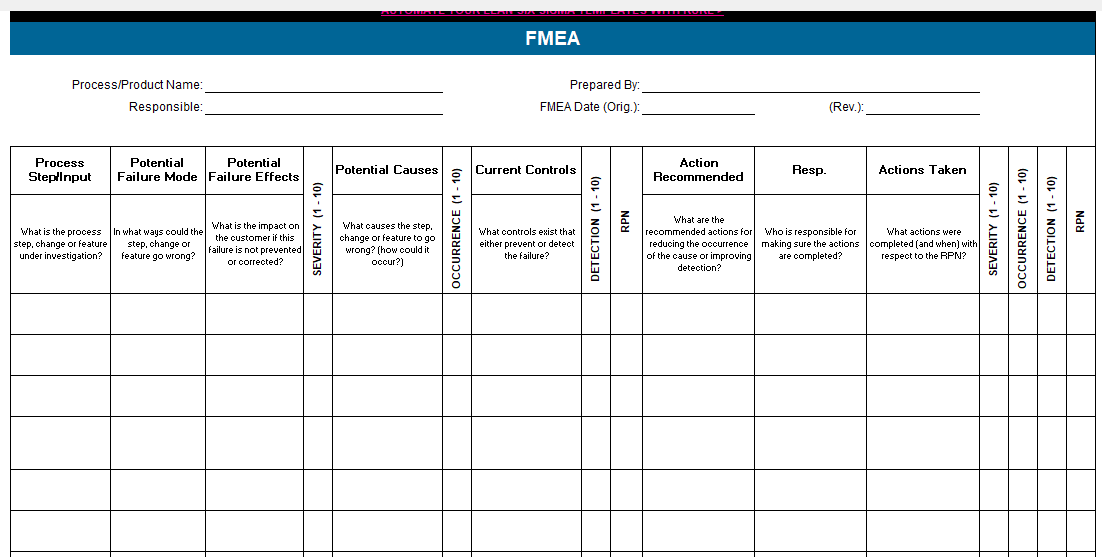
Source: https://goleansixsigma.com
Sample Actual FMEA
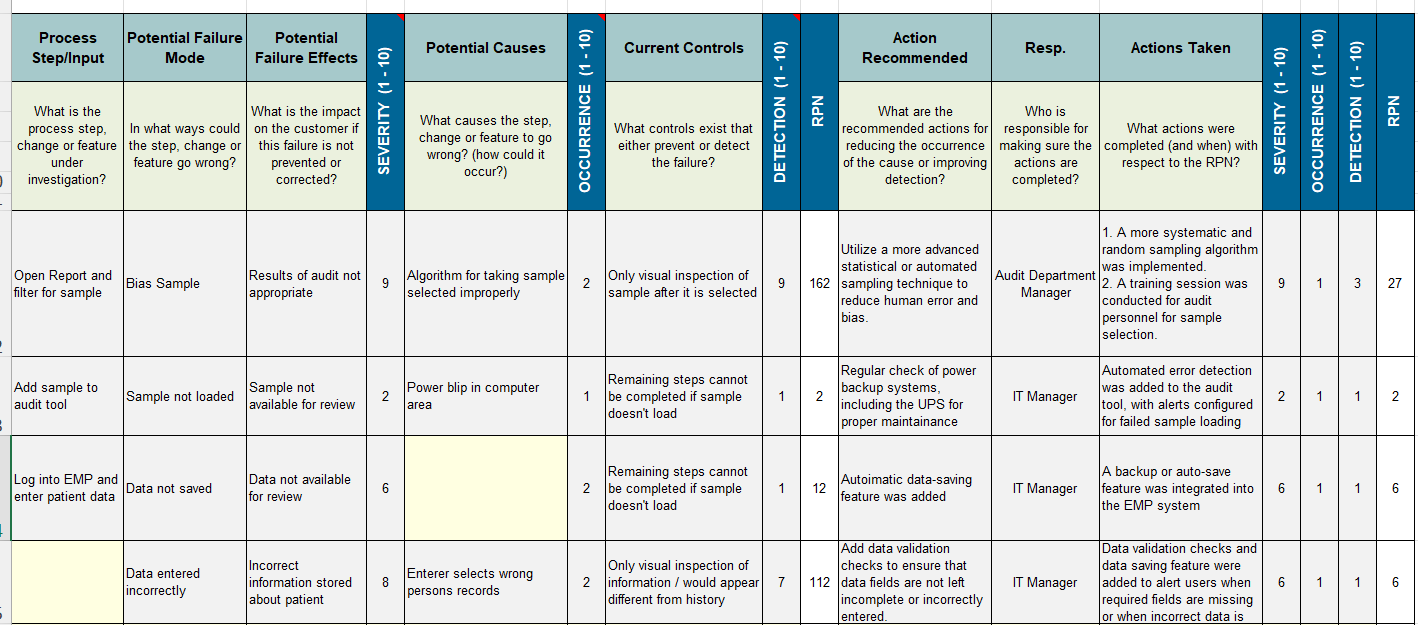
Source: https://goleansixsigma.com
References:
- Department of Budget and Management (2012). Philippine Government Internal Audit Manual. https://www.dbm.gov.ph/wp-content/uploads/2012/03/PGIAM.pdf
- IHI (n.d.). Patient Safety Essentials Toolkit: Failure Modes and Effects Analysis (FMEA). https://www.ihi.org/sites/default/files/SafetyToolkit_FailureModesandEffectsAnalysis.pdf
- GLSS (2025). Template: Failure Modes & Effects Analysis (FMEA). GoLeanSixSigma.com https://goleansixsigma.com/failure-modes-effects-analysis-fmea
- CMS (n.d.). Guidance for Performing Failure Mode and Effects Analysis with Performance Improvement Projects. https://www.cms.gov/medicare/provider-enrollment-and-certification/qapi/downloads/guidanceforfmea.pdf
- Gupta, P. (2005). The Six Sigma Performance Handbook. The McGraw-Hill Companies Inc. USA.